By combining Danish technology and know-how with a concrete challenge of handling large amounts of sugarcane waste in Peru, we are developing a modular building system based on digital production technologies. The building system is initially aimed at temporary construction, but the ambition is to eventually develop modules for permanent structures. The project is an international collaboration between seven partners and combines three areas of innovation: modular architecture, new material technologies and digital fabrication.
2023
Converting fibre-based organic residual waste into recyclable building materials
Trifolium, Advance Nonwoven, CBS, Force Technology, Lilaw Legal Consultancy and A. Münter & CIA EIRL
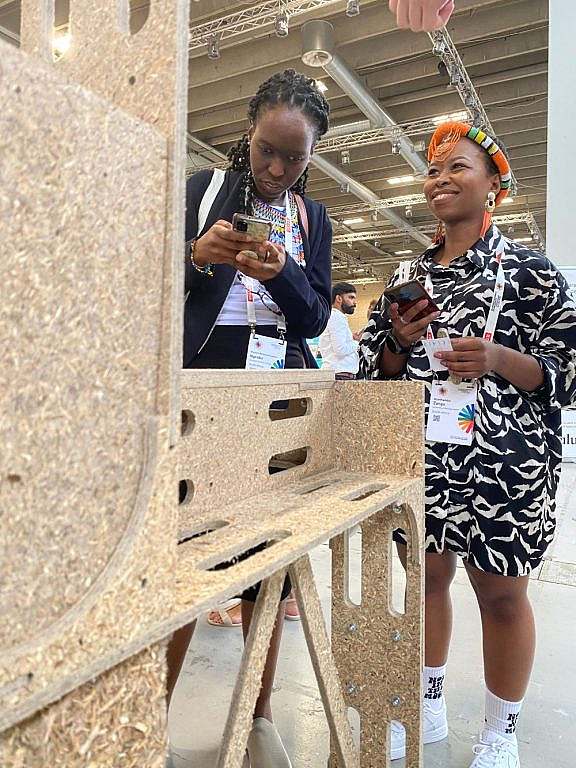
Development of a modular building system via digital fabrication technologies
While the technology to convert agricultural waste products from the sugar industry into new sustainable materials has already been developed, tested and validated, relevant and compelling use and business cases are needed to bring these products to market. That's why visom has brought together an international circle of partners with the ambition to showcase and develop the possibilities of material conversion technologies for the construction sector.
By combining Danish technology and know-how with the current challenge of sugarcane waste management in Peru, we are developing a modular building system based on digital fabrication technologies. While the building system is aimed at temporary construction in the early stages of development, the ambition is to eventually develop it into modules for permanent structures.
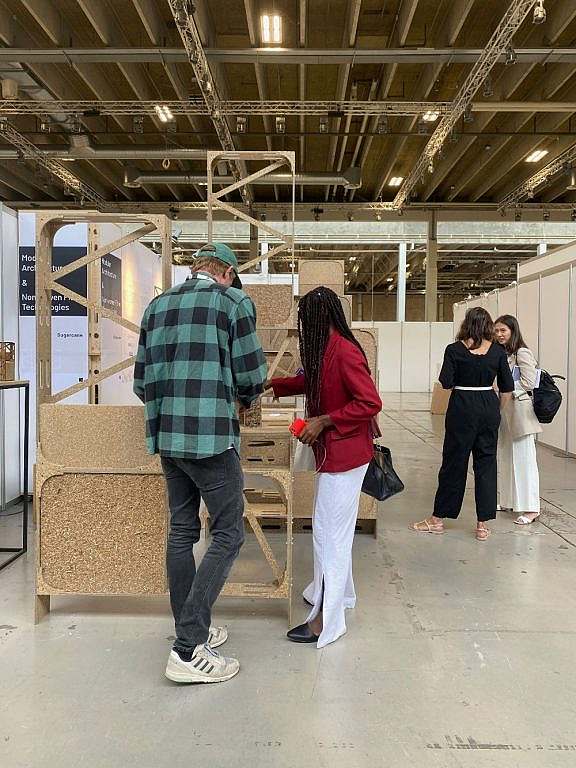
Modular construction
Modular design and construction is an approach where a structure or building is assembled from smaller prefabricated components or modules. Modular construction is often considered to be faster and cheaper than conventional construction methods. While this is often the case, there are also challenges associated with current models in the modular construction industry.
The majority of modular construction is based on production and assembly in large factories. The manufacturing process is typically based on two main strategies. One is to fit large steel boxes with walls and decks, and the other is to construct wall, ceiling and floor elements and assemble them into a closed structure. Once the modules are complete, they are transported to the construction site and assembled. However, these modular construction strategies are associated with relatively high transport costs due to the high volume of modules and, to some extent, fewer design options for both architect and occupant.
Local, digital fabrication of building modules represents a decentralised alternative to these forms of production, where modules can be produced and assembled on site with very high precision. At the same time, digital fabrication allows for parametric design, offering relatively high flexibility in production strategies and optimisation.
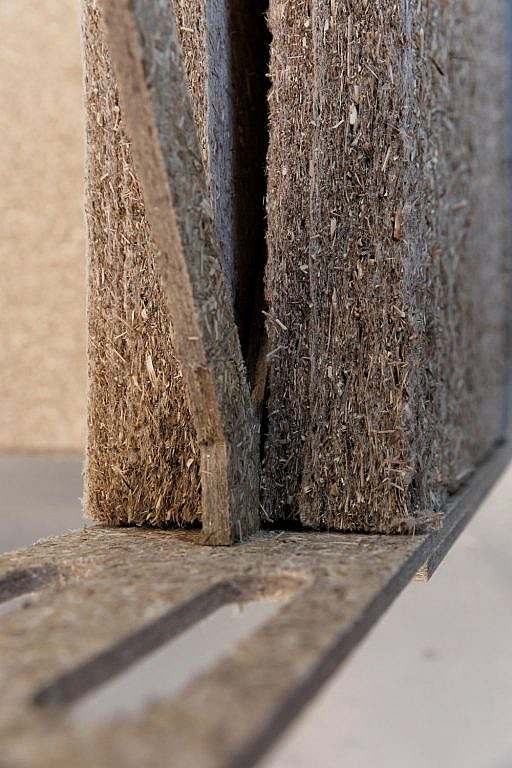
Fibre-based materials with high recycling potential
Construction materials are a $1 trillion global industry, and materials usually account for more than half of the total cost of projects. Traditional materials such as concrete, cement and asphalt make up the majority of this demand (McKinsey & Company 2016). If we want to contribute to a sustainable future, we need competitive alternatives and new possibilities for construction and design.
Non-woven technology opens up the possibility of producing sustainable building materials directly from waste materials and natural fibres, such as hemp, flax, wood, cotton, peat moss, flaxseed and recycled paper, textiles, mineral wool, glass, carpets, tyres, seaweed, etc. Transforming these materials into new building materials can reduce the huge waste of resources across multiple sectors, including construction.
"Non-woven technology has the advantage of converting waste material at the fibre level with very little material degradation. Unlike the reuse of whole building elements (e.g. slabs, bricks and frames), fibre-based materials can be reused and redesigned more flexibly, helping to increase material circulation in the construction sector.
The material used in this project is primarily sugarcane-based due to its promising structural properties and to help solve an environmental and social challenge in Peru. However, the technology is ready and tested with different materials, allowing for local sourcing. Locally sourced materials in a Danish context could be, for example, seaweed, wood, crop residues or paper.
From waste to building material
The construction sector contributes almost 40% of total CO2 emissions. Within the construction sector, there is therefore a great need to transform material that is otherwise considered waste into productive building materials.
This innovation project develops a method to transform fibre-based residual waste into recyclable building material.
Specifically, work has so far focussed on residual waste from Peruvian sugar cane, which is one of Peru's most important agricultural products. Open burning of sugarcane residues is a major challenge in the country, both because of the significant CO2 emissions and the negative health effects for agricultural workers and people in neighbouring villages when they are enveloped in smoke.
By converting the fibrous plant material into materials that can be used, for example, in the construction industry, there will be a significant environmental benefit.
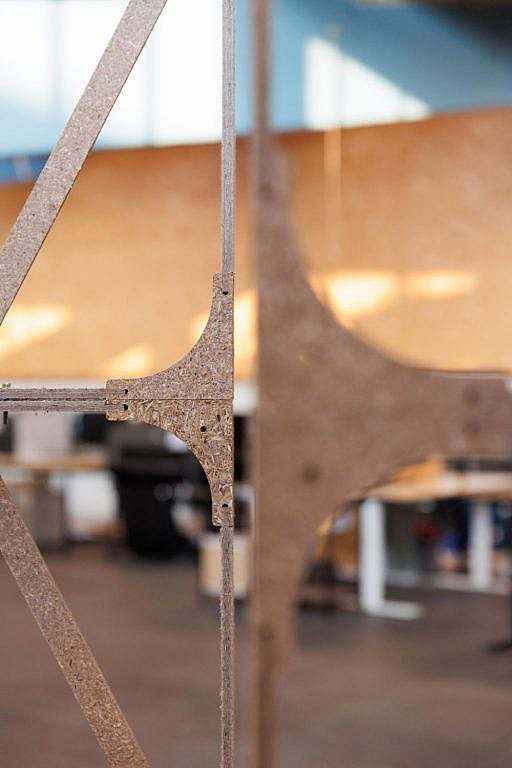
A technology that is widely applicable and localised
By exploring the potential of sugarcane fibres for building materials, we want to promote the use of regenerative building materials and adaptable designs, while primarily using local materials. The material conversion technology makes it possible to use a wide range of fibres from bio-waste, such as coconut, corn husks, bark, etc. This means that local resources can be used for local construction, further reducing CO2 emissions. Working locally also provides the opportunity to test and validate constructions in real-life scenarios that take into account local conditions and contexts, such as climate, building tradition and culture.
Such real-world cases can yield results in terms of policies that drive the adaptation and evolution of regulatory processes that may currently hinder the use of new materials in the construction sector.
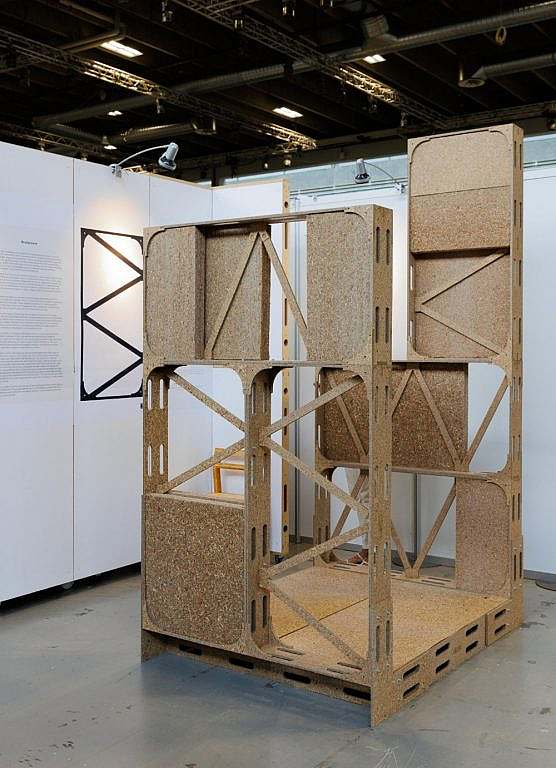
Digital fabrication
The construction industry is among the least digitalised and has yet to embrace new digital technologies that require upfront investment, even though the long-term benefits are significant (McKinsey&Company 2016).
Labour productivity in the construction industry has been stable or declining for the past 25 years. Meanwhile, labour productivity in the overall economy has increased by around 40%. The manufacturing industry worldwide invests an average of 6-8% of their turnover in research and development (R&D). The majority of architects, contractors and construction service providers have either a minimal budget or no budget at all for R&D. Due to this lack of innovation, price has become the main selection point for customers. But this competitive situation carries the risk of becoming a race to the bottom. Not only at a high cost to the quality of our built environment, but also to our quality of life and our ability to build sustainably.
Digital modelling and fabrication is a design and manufacturing process that combines computer-aided design (CAD), such as 2D drawing and 3D modelling, with computer-aided manufacturing (CAM), such as additive and subtractive manufacturing. Additive manufacturing is also known as 3D printing, while subtractive manufacturing can be referred to as machining.
The manufacturing method used to produce the modules for this project is based on CNC technology. Today, these technologies have evolved to the point where they have the potential to change the construction industry. Potentially, this means that it becomes possible to establish local production close to material resources and use local expertise and labour, while radically reducing the costs and environmental impact of long-distance transport.
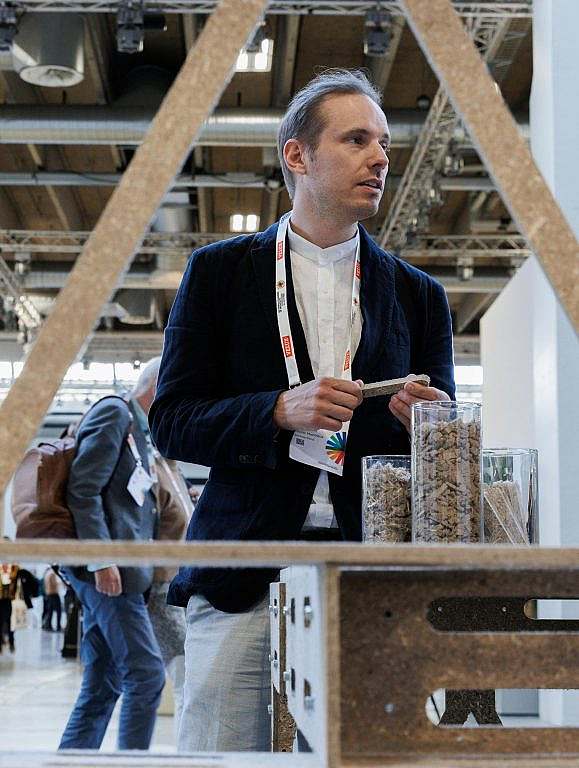